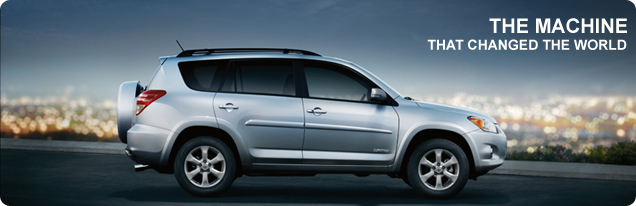
Introduction
• ¡°A system that consists of numerous programmable machine tools connected by an automated material handling system"
• A flexible manufacturing system can produce an enormous variety of items
• An FMS is large, complex, and expensive Computers run all the machines that complete the process
• Not many industries can afford traditional FMS hence the trend is towards smaller versions call flexible manufacturing cells
• Today two or more CNC machines are considered a Flexible Manufacturing Cell (FMC), and two ore more cells are considered a Flexible Manufacturing System (FMS)
Four Basic Types of FMS
• Progressive layout: All parts follow the same progression through the machining stations. This layout is appropriate for processing a family of parts and is the most similar to an automated group technology cell.
• Closed-loop layout: Arranged in the general order of processing for a much larger variety of parts. Parts can easily skip stations or can move around the loop to visit stations in an alternate order. Progressive and closed-loop systems are used for part sizes that are relatively large and that require longer processing times.
• Ladder layout: So named because the machine tools appear to be located on the steps of a ladder, allowing two machines to work on one item at a time. Programming the machines may be based on similarity concepts from group technology, but the types of parts processed are not limited to particular part families. Parts can be routed to any machine in any sequence.
• Open-field layout: The most complex and flexible FMS layout. It allows material to move among the machine centers in any order and typically includes several support stations such as tool interchange stations, pallet or fixture build stations, inspection stations, and chip/coolant collection systems.
Advantages
• Faster, lower- cost changes from one part to another which will improve capital utilization
• Lower direct labor cost, due to the reduction in number of workers
• Reduced inventory, due to the planning and programming precision
• Consistent and better quality, due to the automated control
• Lower cost/unit of output, due to the greater productivity using the same number of workers
• Savings from the indirect labor, from reduced errors, rework, repairs and rejects
Disadvantages
• Limited ability to adapt to changes in product or product mix (ex. machines are of limited capacity and the tooling necessary for products, even of the same family, is not always feasible in a given FMS)
• Substantial pre-planning activity
• Expensive, costing millions of dollars
• Technological problems of exact component positioning and precise timing necessary to process a component
• Sophisticated manufacturing systems
Mixed-Model Assembly Lines
• Some manufacturers changed their forecasting techniques to account for this
• The problem with the traditional layout is that it does take into account consumers change in demand
• Others adopted a mixed-model assembly line technique instead
• There are several steps involved in a mixed-model assembly
• The first step is to reduce the amount of time needed to change over the line to produce different models
• Then they trained their workers to perform a variety of tasks and allowed them to work at more than one workstation on the line
• Then the organization must change the way the line is arranged and scheduled
• There are also several factors to consider in designing a mixed-model assembly line
Line Balancing
U-shaped lines
Flexible workforce
Model sequencing
Line Balancing
• In a mixed-model line, the time to complete a task can vary from model to model
• When planning the completion time an array of values is used
• Otherwise, mixed-model lines are balanced in much the same way as single-model lines
U-shaped lines
• To compensate for the different work requirements of assembling different models, it is necessary to have a flexible workforce and to arrange the line so that workers can assist one another as needed
• Efficiency of the assembly line can be improved with a u-shaped line
Flexible workforce
• Although worker paths are predetermined to fit within a set cycle time, the use of average time values in mixed-model lines will produce variations in worker performance. Hence, the lines are not run at a set speed. Items move through the line at the pace of the slowest operation
Model Sequencing
• Since different models are produced on the same line, mixed-model scheduling involves an additional decision--the order, or sequence, of models to be run through the line
• Another objective in model sequencing is to spread out the production of different models as evenly as possible throughout the time period scheduled

» More Information